Triflex, the line of bi-oriented barrier films, thin and sustainable
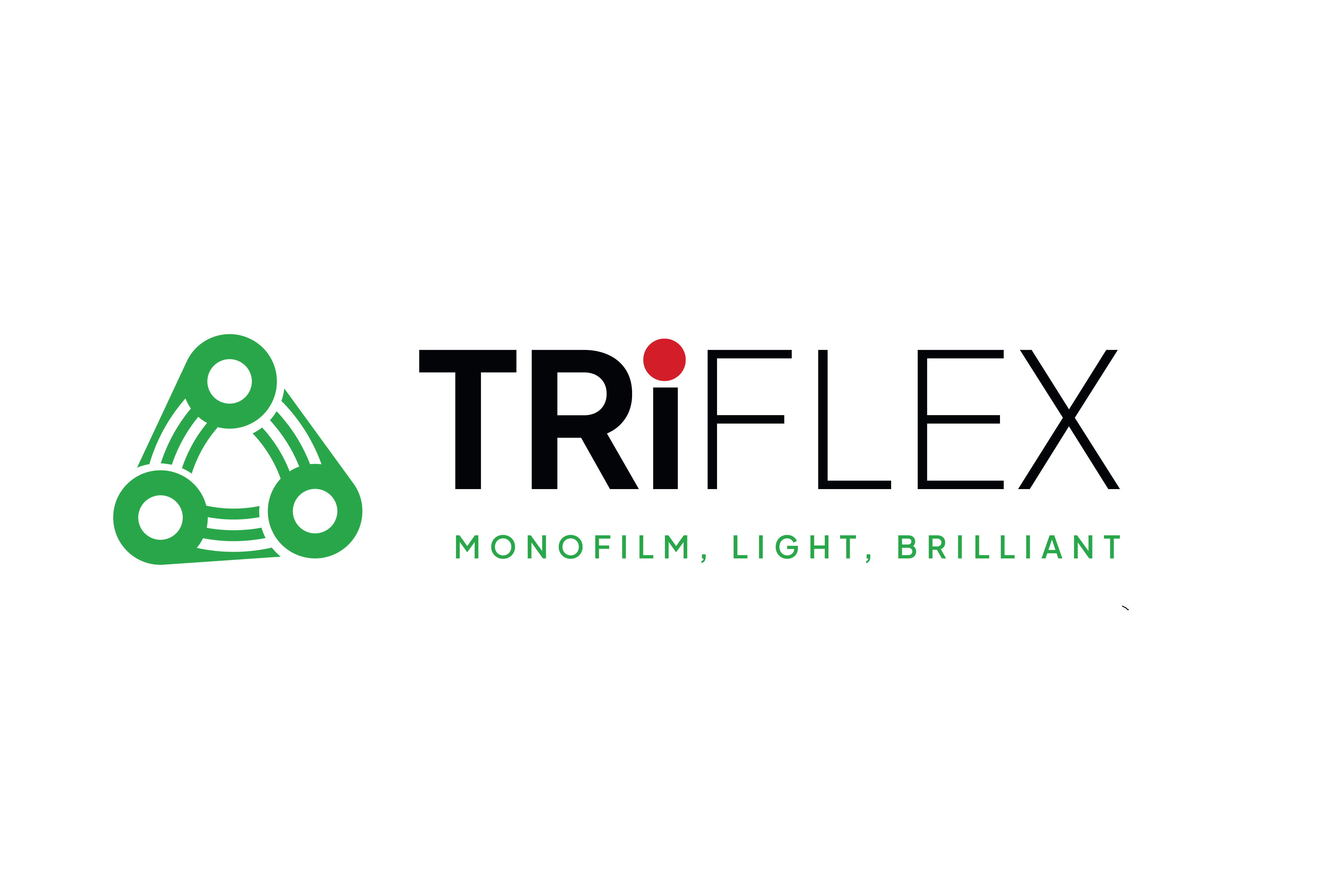
ITP introduces Triflex, the innovative series of coextruded bi-oriented barrier films created with a cutting edge manufacturing system, setting the new era of food packaging: thinner, lighter films with reduced carbon footprint.
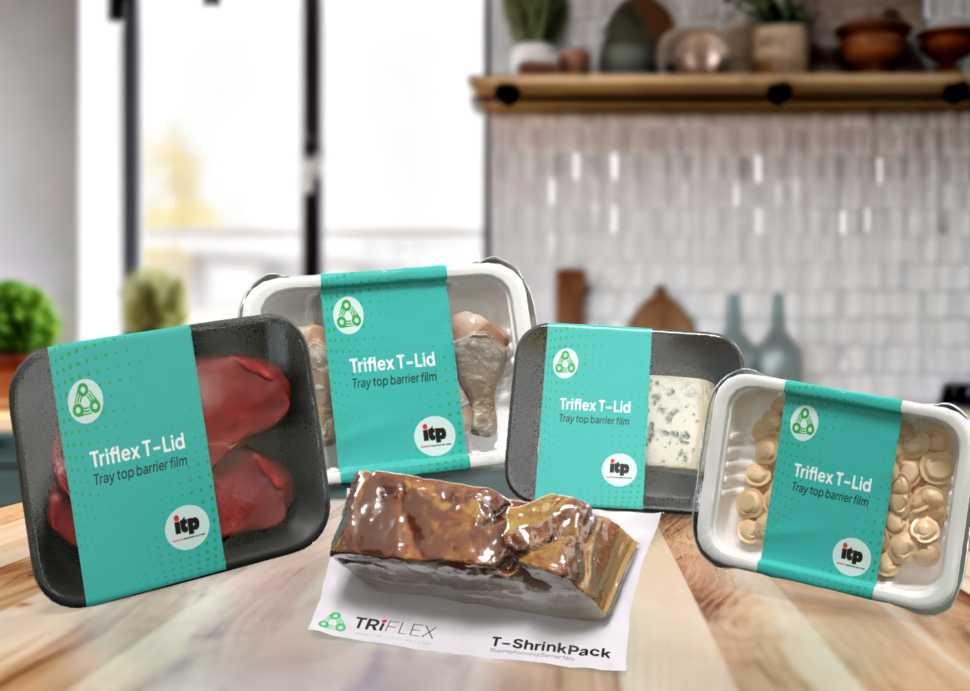
Triple Bubble® extrusion is a cutting-edge technology that can guarantee a series of advantages to the Triflex films produced by ITP:
- Reduced thicknesses
- Excellent mechanics in both directions
- Excellent optics
- Controlled heat shrinkage
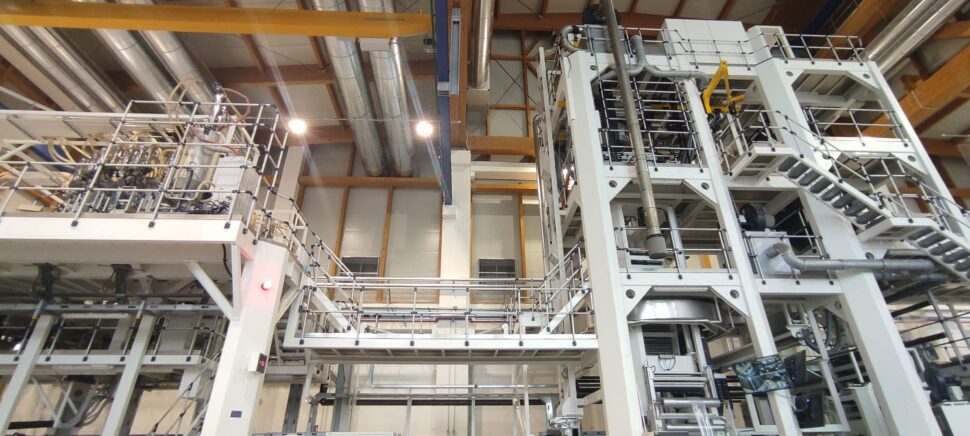
Why pack food with Triflex?
Choosing bi-oriendetd barier films from the Triflex line means ensuring the highest quality available on the market, thanks to the advanced technology and know-how matured by ITP over 50 years in the field of plastic film production using the blown film extrusion system.
Triple Bubble® production gives the new Triflex films three main strengths:
MONOFILM
Triflex films are coextruded, so they do not have to be laminated to acquire special mechanical and functional characteristics.
LIGHT
The 30% reduced thickness compared to laminated films makes Triflex products lighter and reduces their bulk.
BRILLIANT
The three-bubble extrusion makes Triflex film extremely bright, for optimal performance in food packaging.
Triflex films are sustainable both ecologically and economically, because they eliminate the lamination step; the reduction in film thickness results in lower material consumption and therefore a reduction in the carbon footprint. There are many advantages that Triflex products bring to the customer due to their reduced thickness – and therefore reduced weight and bulk: the space required for storage by the customer is reduced; given the lower weight, transport costs are reduced as well as the environmental contribution compared to traditional film.
Triflex products are ideal when a high barrier to oxygen is needed; this application, typical of films produced with this technology, which combines high transparency with good thermoformability and high puncture resistance.
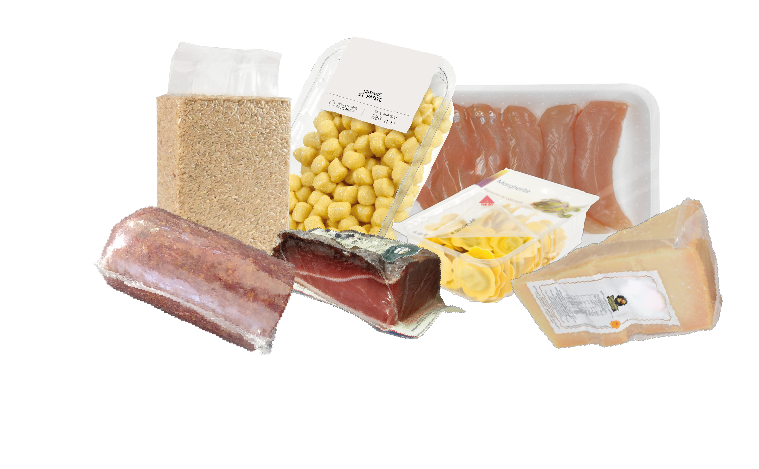
This preservation technique extends the shelf life of sausages, meat, fish, poultry, cheese and rice and is considered the packaging of the future, in line with the need to reduce food waste.
In addition to top and bottom film for thermoforming, the Triflex line includes Lid films for tray tops.
The multiple applications of Triflex are an expression of its flexibility, which is also a founding characteristic of ITP itself: since its origins in 1972, Industria Termoplastica Pavese has aimed at fully satisfying its customers and strives, through the activities of its Research and Development laboratory, to create solutions that perfectly meet their needs in terms of performance, healthiness and quality.
All the benefits of Triflex films
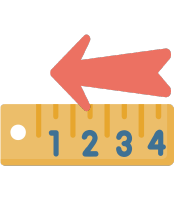
30% reduced thickness
ITP film is ultra-thin while maintaining unchanged mechanical and optical properties.
In this way we reduce the input of plastic into the market.
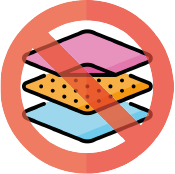
Coextruded monofilm
The new coextruded film turns out to be a thinner and lighter solution than laminated films with the same properties. The environmental contribution is also reduced.
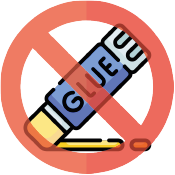
No use of adhesives
The production line allows the extrusion of multilayer films using any type of polymers, avoiding adhesives for increased food safety.
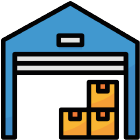
Less storage space
The 30% reduction in thickness also brings benefits in terms of logistics, due to the reduction in space requirements.
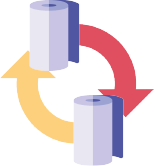
Reduced downtime
For the same footprint, these reels count
30% more product, reducing interruptions
to replace them.
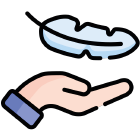
Savings on transportation costs
A product packed with lighter packaging ensures that shipping charges for marketing are reduced.
The bi-oriented barrier film extrusion system
Triple Bubble® technology for the production of bi-oriented barrier films takes its name from the series arrangement of three bubbles that give the film the required prerogatives.

To house the new production line, ITP erected a purpose-built factory, which was inaugurated in June 2023 to celebrate the company’s 50th anniversary.
The machinery is about 20 meters high and 30 meters long.
Its special features:
- Fully automated workflow (4.0): all machine parameters are recorded for SMEA/SMED traceability and analysis
- Thickness gauges for consistent film quality
- High cooling capacity for increased film transparency
Features of ITP’s production line for Triflex films
- 20 m high by 30 m wide
- layers coextruded with any type of polyolefins
- width band from 200 to 900 mm
- thicknesses between 20 and 130 μm